旧ホームページの製作記事の移植です。他の記事も順次移植中です。
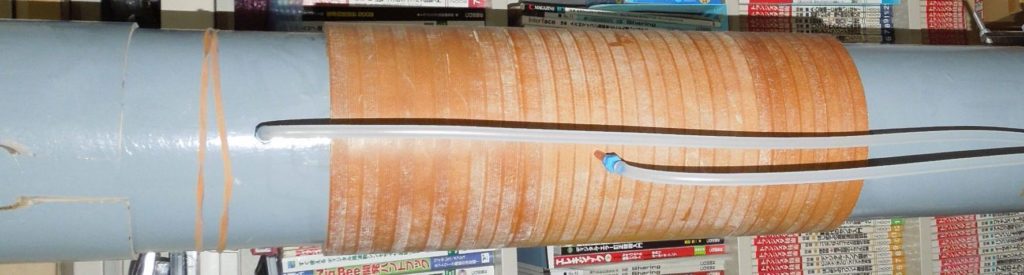
風量計がほしい
風量を扱う機器の委託業務があり、出荷検査のため基準計が必要でした。それまで大エンド様の試験場で校正した「神様」との比較で何とか切りぬけてきましたが、製作・検査はユーザーからは丸投げで特に指示もなく、酷使した老齢「神様」も心配です。それでは、と自分用の基準器を作ることにしました。
また風量は中心部分の風速を測るなどいろんなアプローチで測定可能ですが、直管長さが必要です。いかんせん使ってる風洞が短い(2m)でどれが真値か難しいです。
ベンチュリ型風量計とは
正確には「円すい形ベンチュリ管」と呼ばれ、両端部を円すい状に絞った形状で、入り口と中央部との差圧を換算して風量を得るものです。
標準器としてのJIS規格品はほとんどが特注品で、SUS削りだしや、ダイキャスト鋳造切削品など、とても高価です。
JISハンドブックで寸法を調べる
その構造と寸法はJISで規定されており、JISハンドブックで知ることができます。したがって規格内で製作すれば、規定の値が得られると解釈し製作することにしました。
ただし、規格寸法で製作しても検定受けなければ標準器になるわけでもなく、比較測定の延長に過ぎませんが、常設風量測定器ゼロの状態の脱却です。
常用する風洞は内径φ150mmです。JISによると入口円すい角度は21°固定で、出口円すい角度7~15°(7~8°が望ましい、と書いてあるが無視)したがって出口を15°にすれば最短で製作できることになる。この大きさを加工できる旋盤などないので、板材を積層しながらCNCで加工する方式にしました。
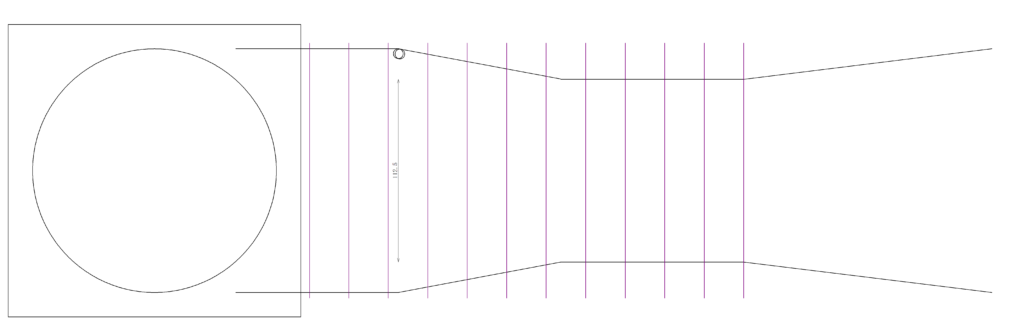
材料は厚さ12mmのMDF。接着剤で積層しながらCNC(2号機)で切削
「材料は何でもよい」のでMDFです。MDFは木材の繊維を圧縮成形した木質ボードです。横方向は強いですが、厚み方向ははがれやすいです。そのため表面だけ接着したものに過度の力で切削すると簡単にはがれてしまい、切削力にも注意です。また、ドライ切削で被削材も繊維質のためかハイスカッターが意外と摩耗するようです。なによりも粉塵がすごいです。
スクエアカッターで荒削りし、φ6ボールで仕上げ。
CNCのZ加工範囲が150mmまでなので、土台いれて12枚積層で1ブロックとしました。一段削ったら上に接着し、荒削り+ボール仕上げ、と繰り返します。すべてCADからNCVCにデータを落としながらで、結構な時間がかかりました。すべては、最終仕上げの手作業を楽にするためです。
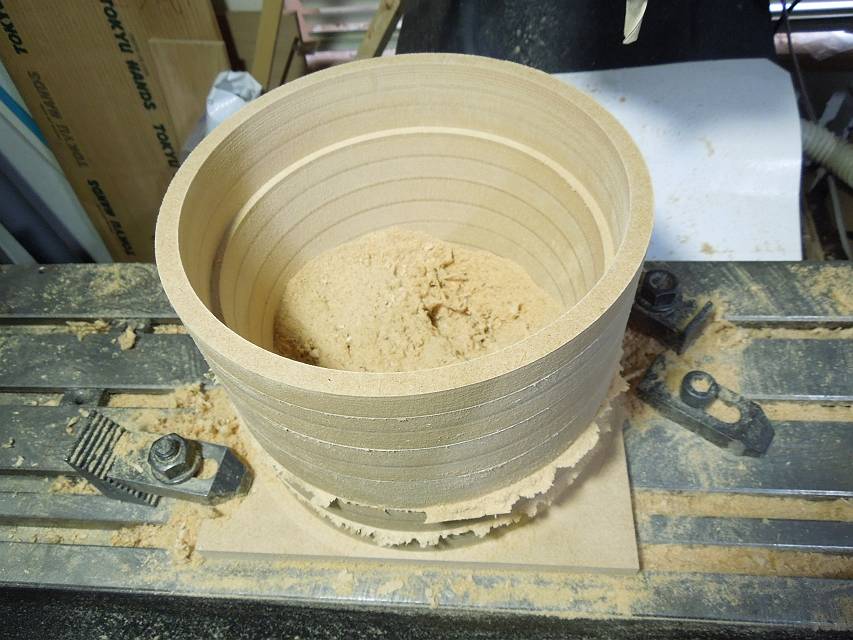
MDF12mmといっても、MAX12.5mmぐらいあり、その都度表面を削って高さも調整します。
要求表面粗さは0.015mm。仕上げは手作業。木固めエースで固め、ウレタンニスで仕上げる。
積層切削したものをさらに積み上げて筒状に仕上げる。ここだけは神経使って同心で積み上げます。内面を手触りがつるつるになるまでペーパーで磨く。ただし、MDFの繊維のため毛羽立つので滑らかになったら固める繰り返し作業です。
MDFは木質なので、セルロースを固着させる「木固めエース」をふんだんに吸収させてしばらく放置。木工品と同じく、塗り・研磨を数回繰り返す。木固めエースは木製のカトラリーの製作に使う木質凝固剤です。本来の使い方ではありませんが・・・。
最後にウレタンニスで仕上げる。JISで規定されている表面粗さはd×10-4=0.015mm以下、指でなでてザラザラ感がなければクリアしているのではないか。
見た目はともかく、内側は樹脂成分でそこそこ仕上がっている。(と思う)
テーパーの様子 見た目はザラザラ感かなり残っているが・・・ 凹凸を減少させ風量抵抗を少なくする。 外側は「それなりに」・・・
性能は!?
とりあえず、年老いた「神様」との比較。5%程度低いようだが、一応「神様」主体で5%低い基準器として使うことにしました。この自作ベンチュリは4年ほど使用。
その後、3%精度の風量計を得る、そして比較
その後、空調界で良く使われているニューエアロアイ風量計をを入手。標準測定器ではありませんが、その総合精度は3%で、購入直後の絶好の機会なので製作ベンチュリ風量計と比較しました。
ニューエアロアイ、新基準器です
直列に接続し、比較したところ、製作ベンチュリは約5%ほど低く出ていました。結局「神様」は年老いても頑張っていたことになります。
ベンチュリ風量計は直管部を必要とします。これも誤差につながっているようです。一方、ニューエアロアイは殆ど直管部を必要としません
5%の違いに3%の測定器、風量や静圧は温度で変化するのでこれ以上の精度要求は無理な上、もともとユーザーから要求はないので「製作ベンチュリ風量計は真値より5%低い」として定期的にニューエアロアイの確認用とすることにしました。
Appendix A:導入部アネモ
風洞のエア入口はアネモ形状が望ましい。それを、FRPで製作。残念ながら製作途中の写真はないが、スタイロフォームをCNCで削り型にして、自作FRPで仕上げたものです。
風洞入口アネモ形状 FRPで作成
Appendix B:FRPでベンチュリを作る・・・とりやめ
バルサを削って、FRP型にしようと思ったものの・・ 表面を仕上げるのに手間がかかり過ぎた
いちおう削り出しベンチュリ風量計の確度が分かったわけですが、違うアプローチでもう一種類できないかと考え、型さえ作ればFRPでベンチュリ風量計作れると思い、木型を作り始めた。「SketchUp」でSTLデータを作り、当時導入した「MeshCAM」にインポートし、実際に削ってみた。
なぜやめたか?。
木型をバルサで作り、FRP積層までいったのだが離形が不十分でバルサ表面がはがれて壊れてしまい、反対側のFRPが作れなかったのである。バルサは多孔質すぎて仕上げが難しく、型作りの時間を考えると、心が折れてしまいました。
結果的にニューエアロアイを導入したので、ボツ企画になってしまいました。
以上