加工機で平歯車を作ろう・・・の後編です。「平歯車を作る 前編」
前編ではモジュール2でデータ作りを始めましたが、もっと小径のφ1エンドミルを想定してモジュール1に変更しました。今回は、歯数Z=100の異型の平歯車をMCナイロンで作成することにしました。
データ作成
前編と同じく、PythonでZ100,m1.0でデータを作成し、CSVファイルを2DCADに読み込ませて作成しました。変更した部分は下記の二行です。
para_z=100 para_m=1
ここで作成したデータを2DCAD(図脳)にインポートさせ、dxfで出力します。
そして、前編と同じく歯底円をエンドミルで加工できる円周に変更すると下図の歯形ができました。
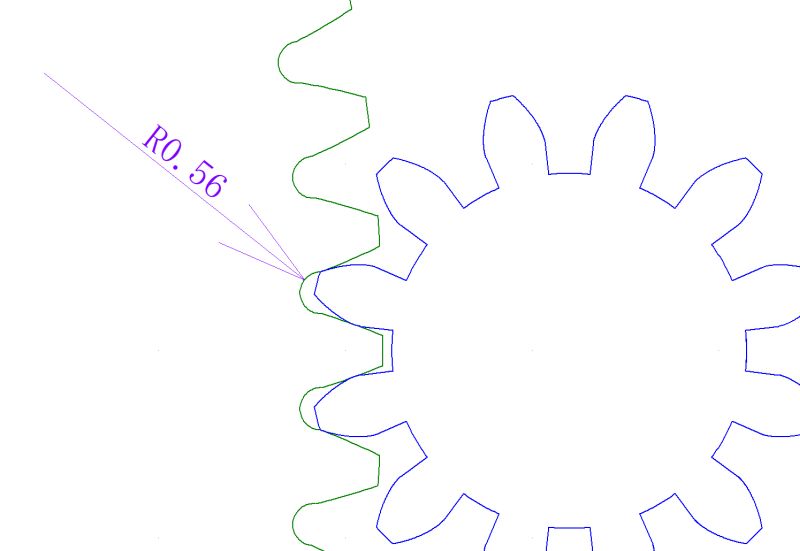
歯先のデータを加工し、材料の面付けをしてφ3、φ2、φ1のカッターパスを描画しました。
今回はφ2のエンドミルは使いません。
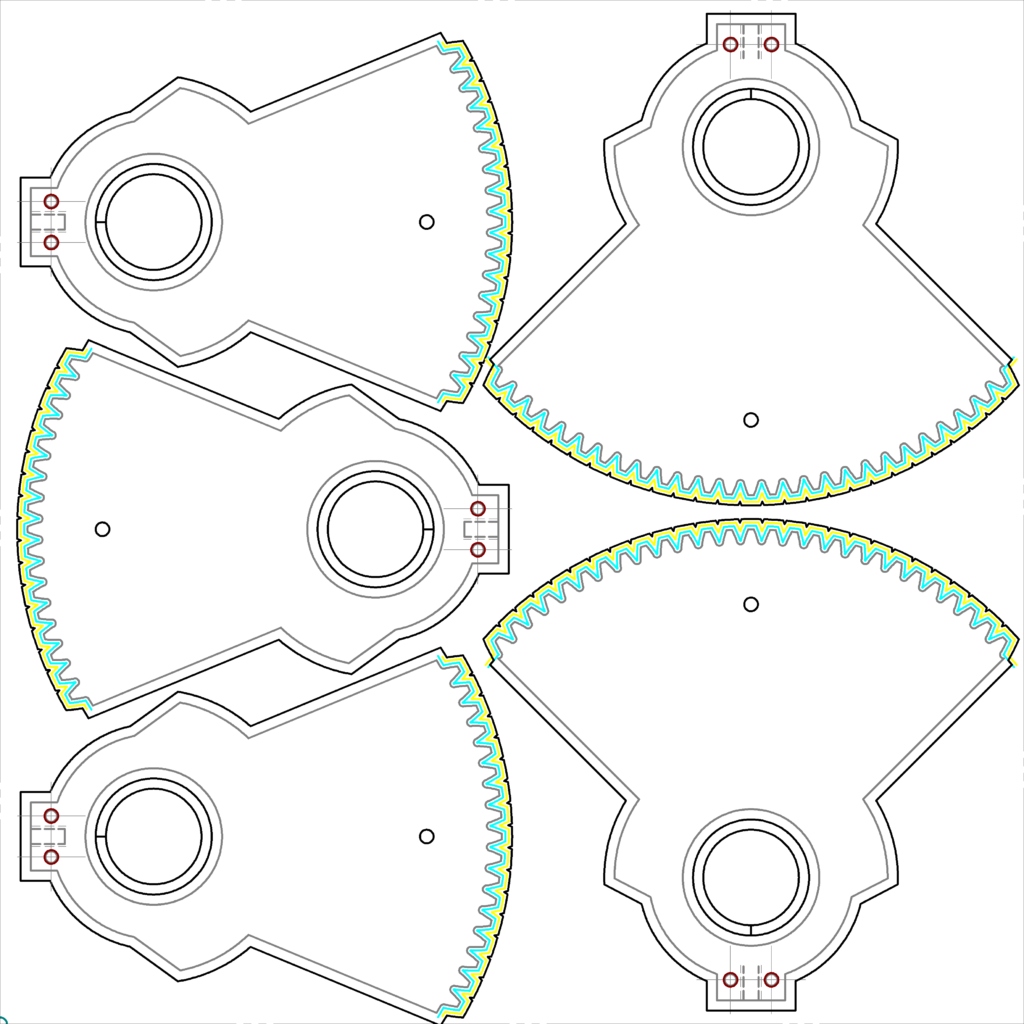
グレー:外形、緑:φ1、黄:φ2、黒:φ3
加工開始
まずφ3mmエンドミルで外形を加工。歯車で言う「ギアブランク」を切削。この時の加工条件は、10,000rpm、F900、切込み1.2mm。
その後、φ1×1.5mm、首下10mmのロングネックスクエアエンドミルにて30,000rpm、F300、切込み0.5mmで歯の加工を開始。
段取りでミス、1枚目を失敗してしまい、完成は2枚ずつの計4枚です。
加工時間
φ3によるブランク加工(ギヤ5枚分):17分
φ1歯面加工(ギヤ5枚分):40分
治具に装着し、段差加工(ギヤ1枚分):一分未満
加工後の仕上げ作業
樹脂の切削でいつも大変なのが、バリ取りなどの仕上げです。POMやABSは比較的きれいですが、ナイロンは角に強靭なバリが発生します。たぶんこのバリをどう抑えるかが、プロとの境目ですね。
案の定、歯面の端には盛大なバリがでたので、バリ取り作業開始。板厚7mmのところ7.7mmもあったので、歯の側面を削る工程をいれました。そのための治具をPOMで作成。
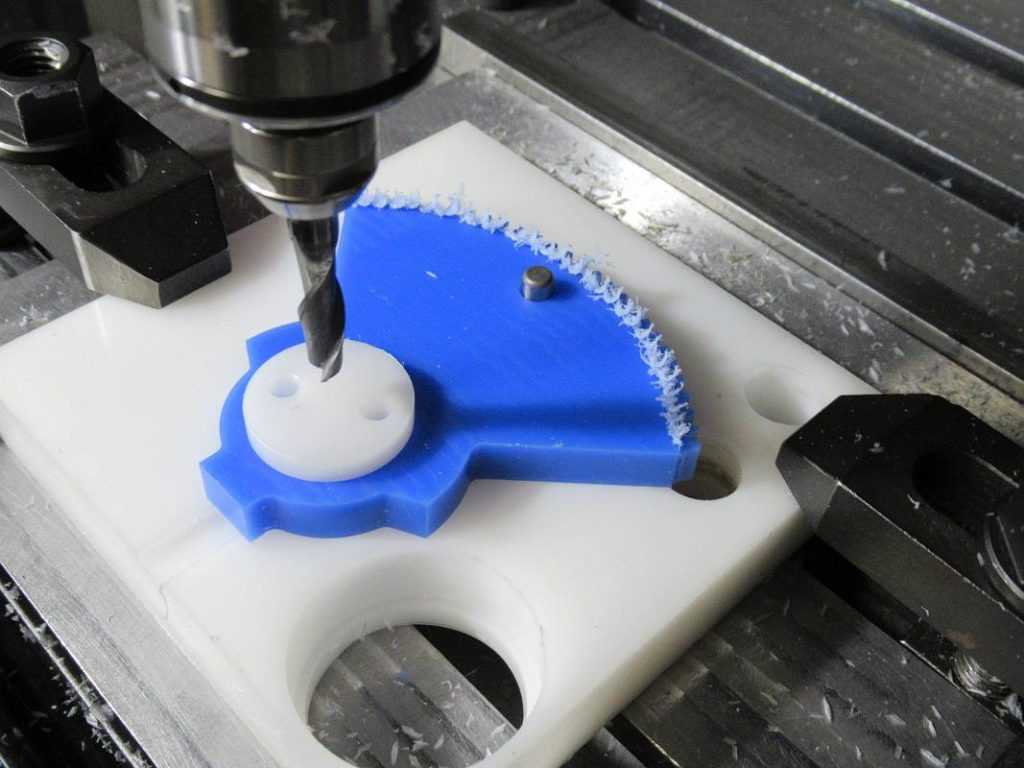
段差切削後のバリはナイフで容易に除去できる 気持ちの良い除去後
ピニオンとあわせてみる
2種類の平歯車ができた
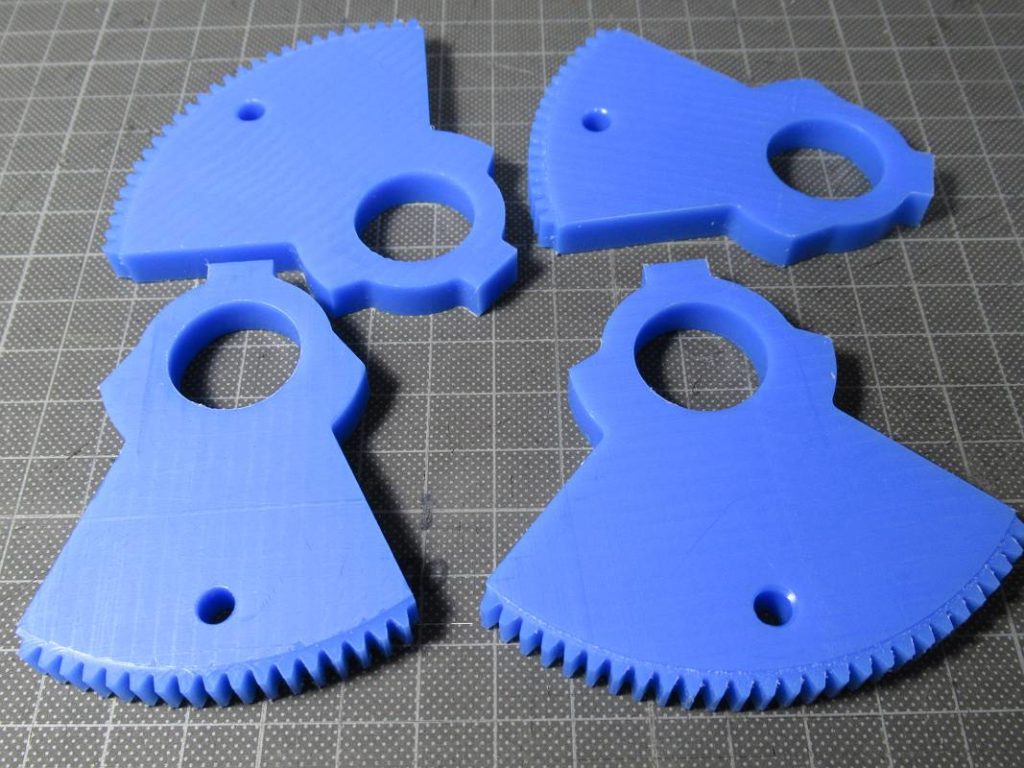
ひとまず平歯車ができましたが、バックラッシを考慮していないので実際に組み込んでから検証です。
小径のロングネックエンドミルは神経を使います。1パスで良いのか、仕上げ切削をいれたほうがよいのか、まだまだ経験不足です。
実はインボリュートカッターもすこしづつ購入しているので、後日報告できると良いです。
以上